3D Printing Unmanned Aerial Vehicles (UAVs)
One of the key factors behind this expansion is the increasing adoption of UAVs in commercial and civil applications, where their ability to perform complex tasks autonomously is proving invaluable. Within these sectors, UAVs are now essential tools for a variety of industries including:
Agriculture:
UAVs, equipped with cameras and sensors, enable real-time crop health monitoring for farmers. Furthermore, customized drones are being used to distribute fertilizers, pesticides, and water to specific areas in a field, reducing waste and improving crop yield.
Healthcare:
UAVs are being utilized to safely deliver medical supplies to hard-to-reach areas thanks to sensor technology and artificial intelligence. These same technological advancements are driving the logistics industry to capitalize on UAVs for last-mile delivery solutions. This was particularly pertinent during the COVID-19 pandemic, where companies sought contactless delivery methods to minimize human interaction. UAVs played a crucial role in ensuring the continuity of supply chains during lockdowns, which has since led to a permanent increase in their use in the logistics sector.
Combat and Surveillance:
The ongoing conflict between Russia and Ukraine has spurred the development and deployment of military UAVs, as nations seek to enhance their surveillance and combat capabilities. For instance, in June 2023, the Royal United Services Institute (RUSI) report, a British firm specializing in defense issues, stated that the Ukrainian army was losing over 10,000 drones a month, or over 300 in a single day.
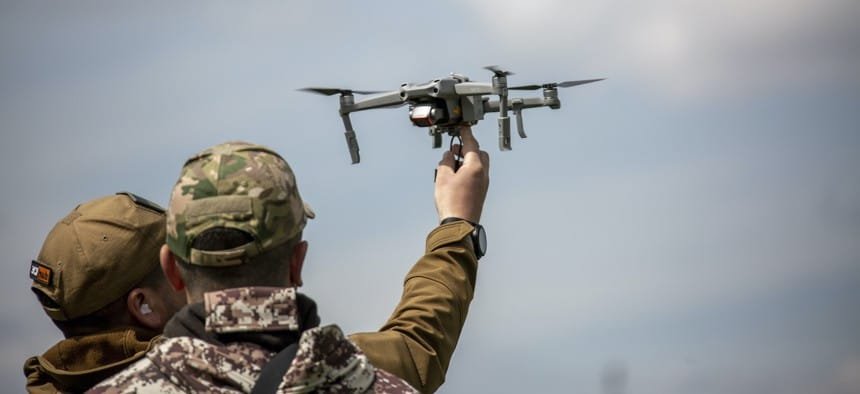
Ukrainian trainees flying a bomb-carrying drone. Narciso Contreras / Anadolu Agency via Getty Images
3D Printing in UAV and UAS Manufacturing
1. Accelerate Time to Market
A prime example of this synergy between 3D printing and the UAV industry is the collaboration between Unusual Machines and HP’s Multi Jet Fusion (MJF) technology. Unusual Machines has been using MJF 3D printing to produce critical UAV components such as hoops, connectors, and other small parts. By leveraging MJF’s ability to create complex geometries, Unusual Machines can mass produce these drone parts, make quick design iterations, and lower part counts. As a result, engineers can quickly adapt to fluctuations in market demands in various industries, accelerating time-to-market for UAV parts.
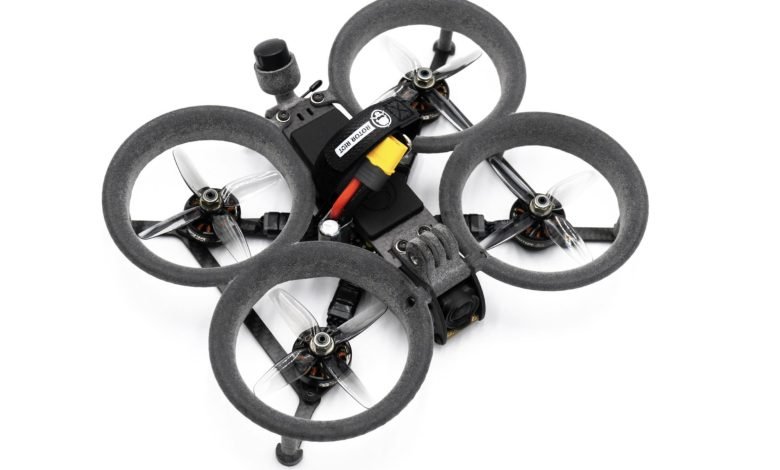
Unusual Machines produces drone components using Multi Jet Fusion 3D printing technology. Image Source: VoxelMatters
2. Cost Efficiency
UAV part manufacturers are also making significant reductions in cost during the design iteration and product testing phase. In conventional manufacturing, creating a prototype for each design iteration often requires new molds, tooling, or reprogramming of CNC machines. These processes are not only time-consuming but also expensive, especially when dealing with intricate designs that are common in UAV components. Each iteration can cost thousands of dollars and take weeks to produce, limiting the number of design cycles that can be feasibly tested within a given timeframe. When using 3D printing, engineers can experiment with different materials, densities, and design features to optimize performance, all without the financial burden of retooling. The ability to produce and test multiple iterations in quick succession allows for thorough validation of designs, reducing the risk of costly errors later in the production process.
Once an engineer moves past the product testing and design phase, 3D printing becomes particularly cost-effective for low-volume production. Traditional manufacturing methods achieve economies of scale with high-volume production However, 3D printing maintains consistent costs per part at varying production volumes. This makes it ideal for producing small batches of parts, especially those with complex geometries that would be costly or impossible to produce using traditional methods. The ability to print complex parts in a single operation, without support structures or assembly, further reduces labor costs and streamlines the manufacturing process.
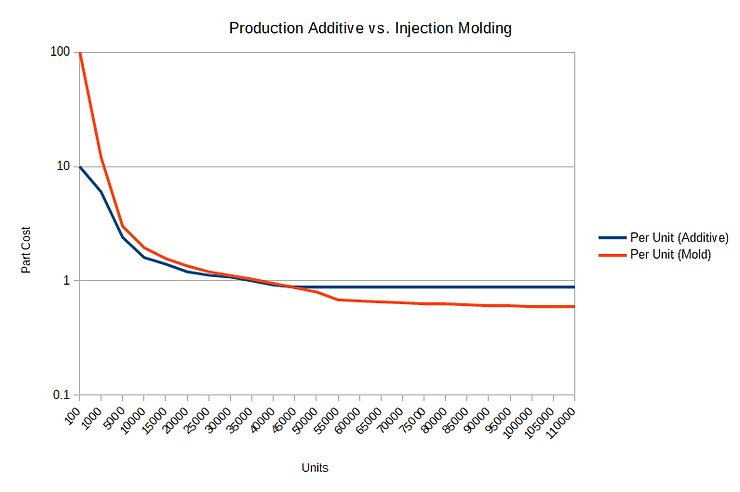
3D printing chart showing consistent cost per unit compared to injection molding. *Note: Exact cost per unit is dependent on the specific 3D printing material and technology used.
3. Enhanced Design Flexibility
One of the ways this balance can be achieved is by producing topology-optimized, lattice-structured components. This method involves generating internal geometries that reduce material density while distributing load effectively across the part. To better test and optimize drone part geometries for lightweighting, engineers can apply various advanced 3D printing infill patterns, such as the “tri-hexagon” and “cubic” structures. These infill patterns directly affect the mechanical properties of the parts, making it a valuable step when trying to meet critical part property requirements. For example, a study comparing various 3D-printed infill patterns found that the “tri-hexagon” pattern offered the greatest stiffness and resistance to deformation under load, making it ideal for drone wings that require structural integrity. On the other hand, the “gyroid” pattern, while lightweight, exhibited higher levels of plastic deformation, making it less suitable for applications where rigidity is crucial. However, the “gyroid” pattern’s continuous and smooth curves provide greater flexibility, making it beneficial for parts requiring a degree of vibration absorption such as drone landing gear.
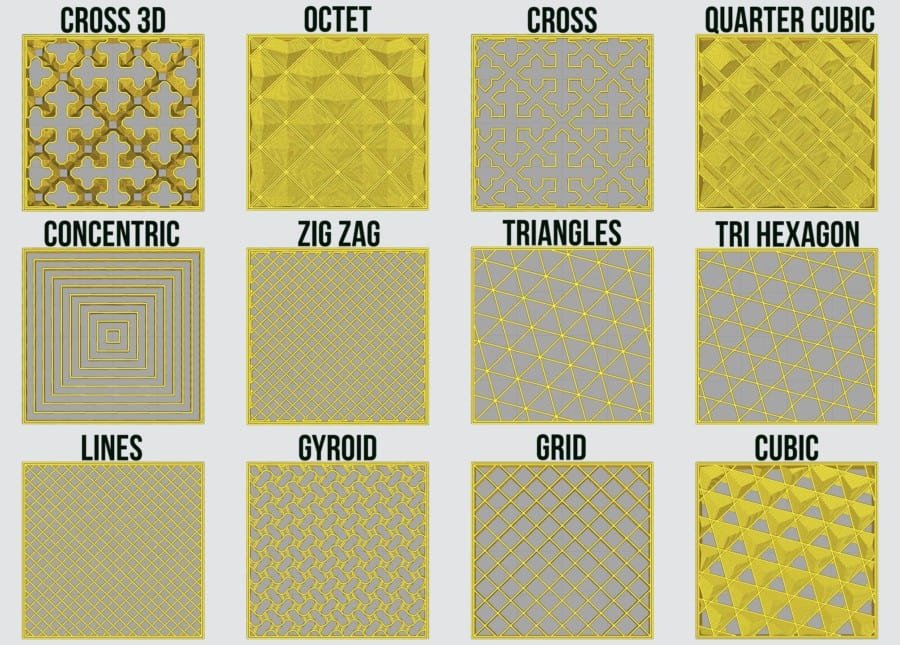
Basic types of infill patterns used in the 3D printing industry
This precise customization of a UAV component is beneficial while leveraging Multi Jet Fusion 3D printing technology, where the elimination of support structures helps optimize part designs. This design flexibility allows engineers to integrate multiple functions into a single part, such as combining structural elements with internal channels for wiring or fluid flow. This not only simplifies the assembly process but also reduces the overall weight and complexity of the UAV.
This flexibility is particularly evident in antenna design and the use of dielectric materials, which are critical for optimizing UAV communication systems. Research shows that 3D printing allows for the creation of complex dielectric structures that significantly enhance UAV antenna performance, improving signal reception and transmission. These advancements are crucial for the reliable, long-range communication essential to successful UAV operations.
Looking Ahead
As a leading contract additive manufacturer, Endeavor 3D offers 3D printing services that streamline production, reduce costs, and achieve quality. By partnering with Endeavor 3D, manufacturers can access state-of-the-art 3D printing technologies and expertise, ensuring that their drone components meet the highest standards of performance and reliability.
Interested in learning more about how 3D printing can elevate your design or production projects? Join us at this year’s IMTS event in Chicago, September 9-14. Visit our booth #433127 to explore our latest advancements in additive manufacturing with insights from our technical experts.