3D Printing Materials for Automotive Applications | Part 1
Factors to Consider Before Choosing a Material
1. Tensile Strength
2. Flexibility and Rigidity
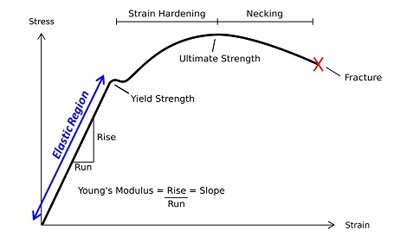
3. Heat Resistance
One common way Endeavor 3D quantifies the heat resistance of plastic to avoid deformation is by evaluating the heat deflection temperature (HDT) using the ASTM D638 test method. This gives us a clear indication of how 3D-printed parts will perform under real-world scenarios. During HDT testing, the level of stiffness is measured to help predict the 3D-printed part’s response to varying loading conditions.
4. Chemical Resistance
After the cooling process, amorphous or semi-crystalline chains are formed that affect the temperature resistance and strength of the polymer. The more crystalline a polymer is, the more resistant it is to aggressive chemicals. The chemical resistance of a polymer is also affected by the presence of fillers and the orientation of the material’s bonds.
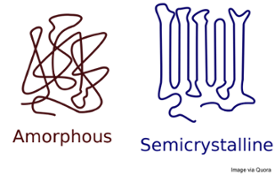
5. Cost
Determining the material properties can help kickstart whether a material is suitable for an automotive application. Once you have a material in mind, the part complexity plays a vital role in determining the cost of your project. 3D printing’s ability to overcome design constraints allows parts to be built at a rapid pace.
At Endeavor 3D, our robust design services help optimize part designs and minimize unnecessary complexities, helping manufacturers reduce costs without compromising on quality. One way this is done is through batch production. 3D printers have build volumes that play a significant role in determining the cost of a project. Our experienced team of designers and engineers work directly with customers to consolidate parts in a way that reduces material consumption, increases printing efficiency, and optimizes part performance.
Summary
Partnering with experienced professionals like Endeavor 3D can significantly ease the selection process. We possess the expertise and resources to not only help you choose the correct material but also optimize your design to minimize costs and maximize performance.
Contact us today for a FREE quote on your next 3D-printed project.