3D Printing Materials for Automotive Applications | Part 2
- Lightweight, yet durable options resulting in improved fuel efficiency and vehicle performance.
- A diverse range of material capabilities and properties to fit your specific application needs.
- A more cost-effective and accessible approach to faster product development times.
In this article, we’ll explore five key polymer 3D printing materials and their transformative impact on automotive manufacturing.
The Automotive Adoption Timeline:
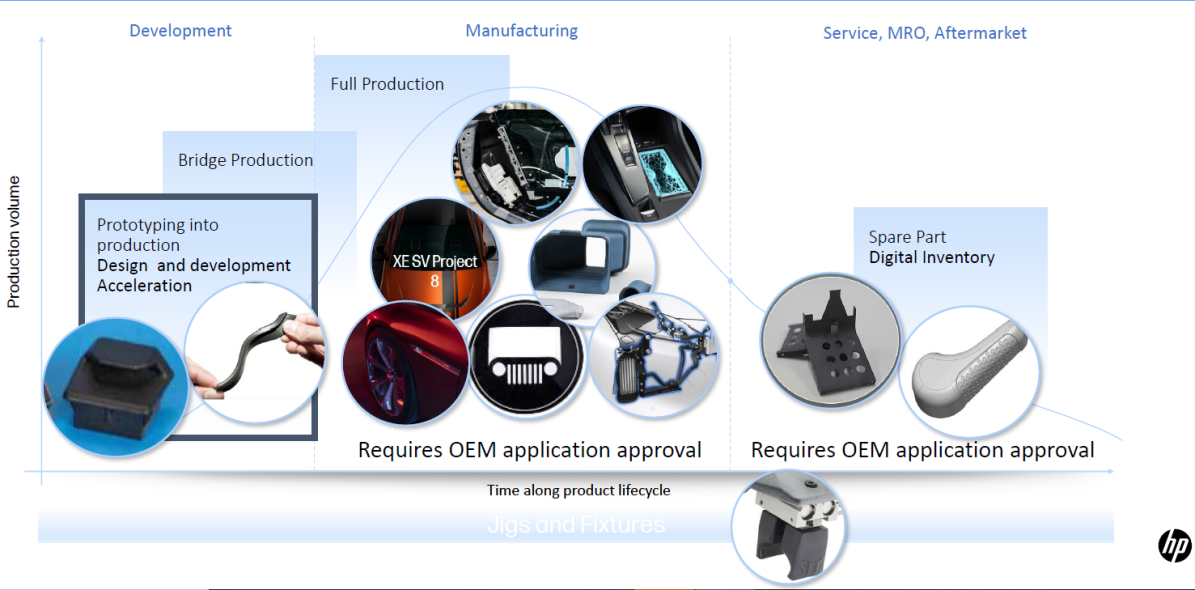
Source: HP
The small-volume production (bridge production) stage is essential to bridging the gap between prototyping and full-scale production. This is especially a sweet spot for contract manufacturers like Endeavor 3D because of their ability to cater to the demand volumes of automotive manufacturers, providing a repeatable and agile bridge to the supply gap.
Once you are ready for full production of your automotive parts it is important to identify materials that offer scalability and consistency to meet the demands of mass manufacturing. However, the process of choosing the right material for end-use parts is different than other stages of the product development lifecycle. Due to the high volume of parts being produced, the total part quantity, material cost per part, and printer build capacity of the technology that is being used should all be considered.
As a vehicle enters the aftermarket phase, the need for replacement parts and repairs becomes increasingly important. Thermoplastic Polyurethane (TPU) emerges as a key material, offering custom-fit sealing systems and flexible hoses and tubing. These replacement parts often require a material that can withstand repeated use and mechanical stress. With a Shore A Hardness rating of 88, TPU exhibits the ideal balance of stiffness and elasticity for components that experience wear and tear over time.
In addition to end-use parts, 3D printing polymers are used to produce jigs, fixtures, and tooling to sustain the manufacturing process. During this phase, high-performance thermoplastics are replacing traditional manufacturing materials. This reduces the time for tooling validation and accelerates the process of identifying where changes need to be made long before end-use parts are created. As a result, factory floor operations are optimized by reducing downtime.
PA12 (Nylon):
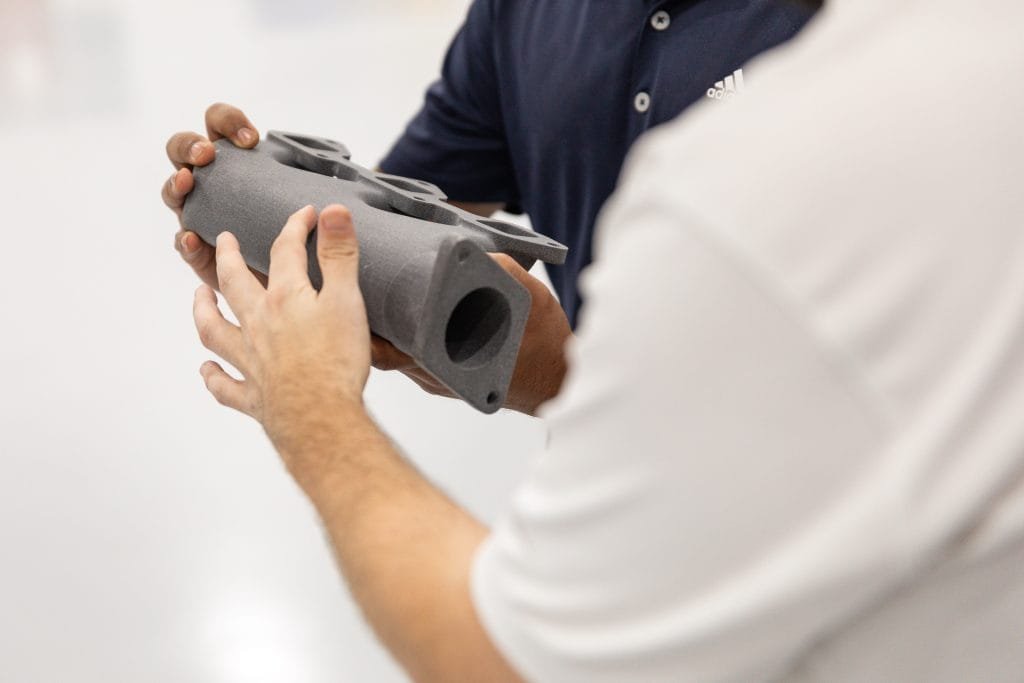
Endeavor 3D PA12 Manifold
ABS (Acrylonitrile Butadiene Styrene):
ABS is also commonly used for end-use interior car components. It offers excellent surface finish and dimensional stability, making it ideal for producing aesthetically pleasing parts with intricate details. However, due to its sensitivity to temperature changes, ABS can experience issues when being used for under-the-hood applications. Compared to PA12, ABS has a Heat Deflection Temperature of between 180 – 215 F at .45 MPa. Proper printer calibration and the use of a heated bed can help mitigate the issue of warping during the 3D printing process. Due to its sensitivity to heat during the 3D printing process, ABS is a popular material among Fused Deposition Modeling (FDM) 3D printing technology. The presence of a heated bed allows for easily molded shapes at the proper temperature.
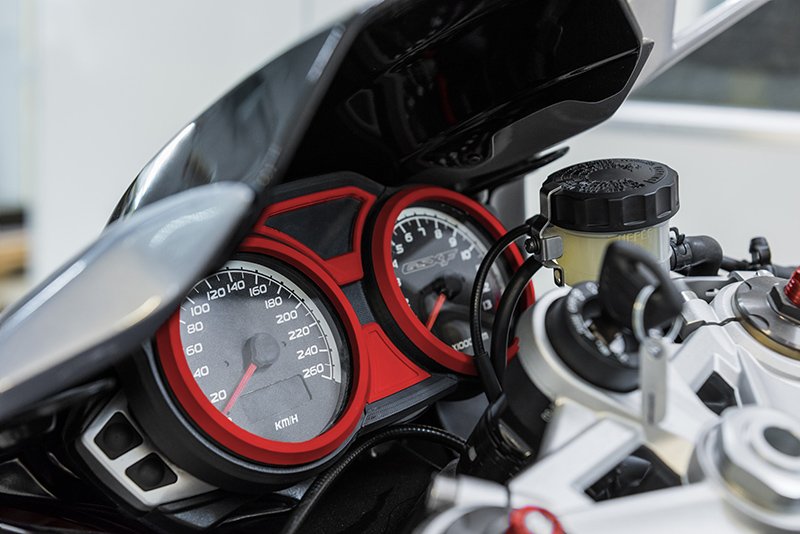
Motorcycle dashboard made of Z-ABS. Source: Zortrax
Acrylonitrile Styrene Acrylate (ASA):
ASA thrives in the small-volume production phase, enabling rapid fabrication of custom parts. The material often caters to niche markets and unique customer needs, given its ability to produce parts with specific mechanical and aesthetic requirements. The material is compatible with Fused Deposition Modeling (FDM), one of the most common 3D printing technologies.
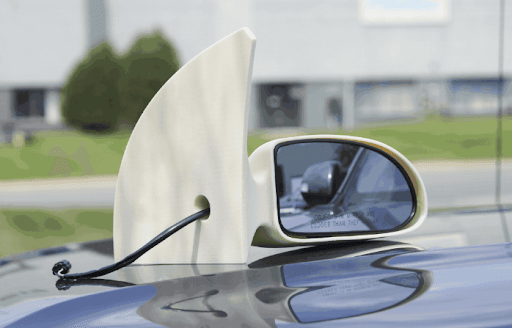
Car rearview mirror printed with ASA
Polypropylene (PP):
So why haven’t we seen a more widespread adoption of polypropylene? Compared to PLA, a common alternative because of its ease in processablity, PP “weighs about 30% less per volume” for end-products while having “about 40% more material per pound of material.” Moreover, it is recyclable and resists deformation when exposed to high temperatures. However, the material’s tendency to warp during the 3D printing cooling process has given it the name “poly-warp-ylene” says Jason Vagnozzi, Commercial Director of Additive Manufacturing & Digital Ventures at Braskem. This has created a headache for many automotive manufacturers because of the inconsistencies associated with 3D printed end-use parts using polypropylene.
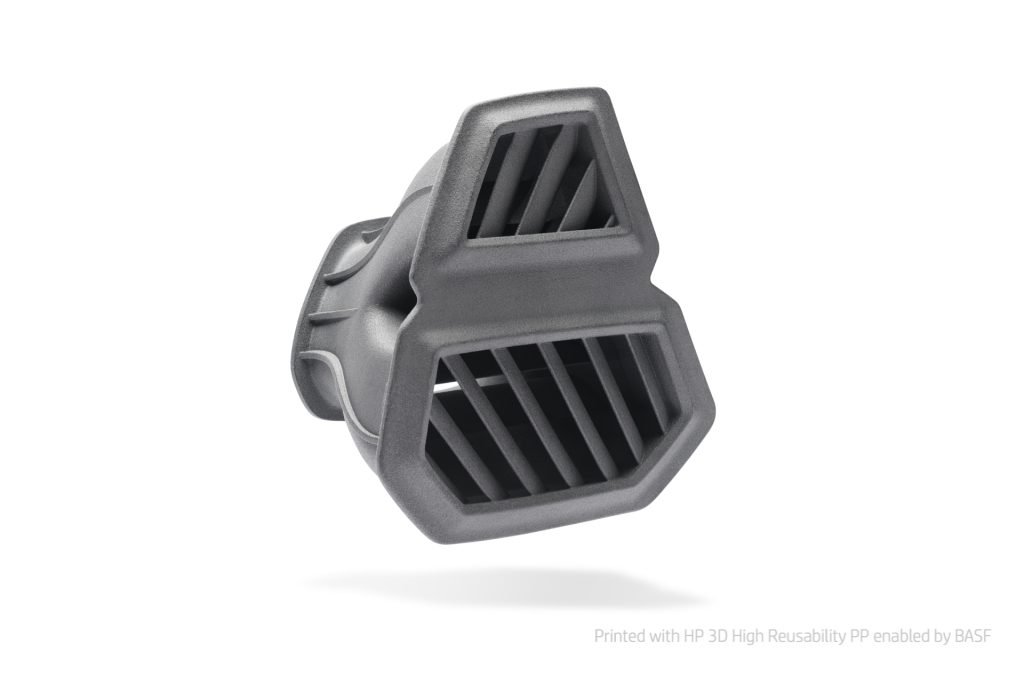
Car door defroster vent printed with BASF PP
Thermoplastic Polyurethane (TPU):
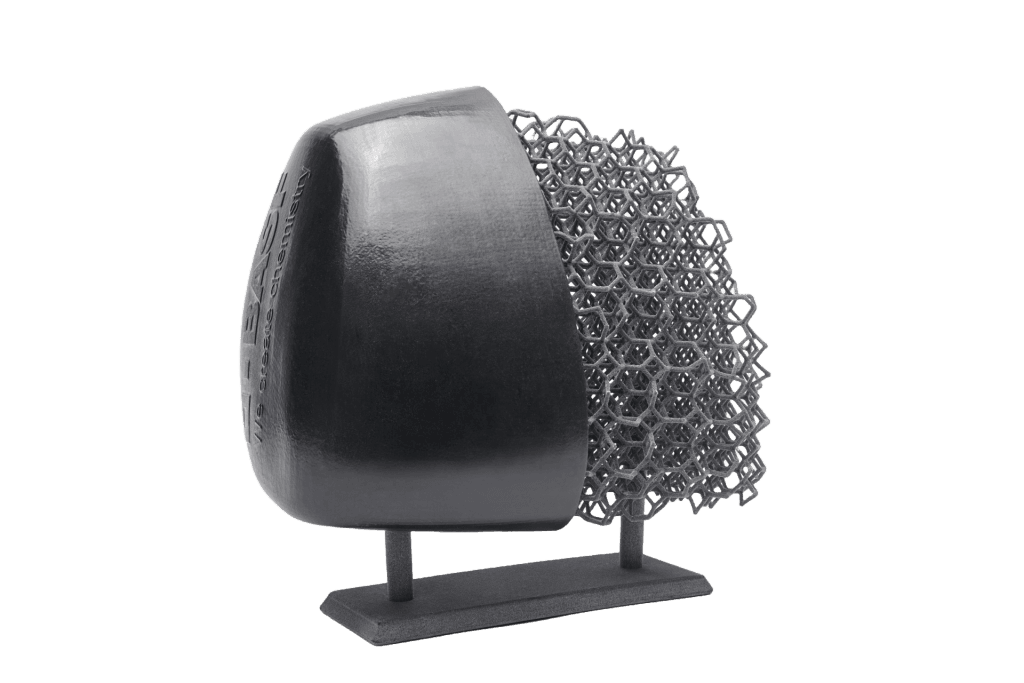
Car headrest with BASF TPU
Conclusion
The 3D printing industry is constantly evolving, with new materials continually emerging to address industry-specific applications. To navigate this dynamic landscape, automotive manufacturers are looking to Endeavor 3D as a trusted partner. Contact us today to explore how you can harness the full potential of 3D printing for your next project.