Nylon PA 12 as a Delrin Alternative
This article explores the nuances of these two materials, delving into their mechanical properties, processing capabilities, and suitability for different applications. Depending on the intended application or project requirements you have in mind, the crucial differences between these two materials may lead you to believe that one is better suited for your specific needs. However, by comparing Delrin and Nylon PA 12, we will uncover why many engineers are considering a shift toward Nylon PA 12, especially when leveraging the advantages of additive manufacturing.
Delrin: A Brief Overview
Delrin is a preferred material for manufacturers using injection molding and CNC machining because it can be machined using 3-axis and 5-axis CNC machines. Although it can be 3D printed, it is not ideal due to its high melting point and significant warping during the cooling phase. This makes it less suitable for complex or intricate designs, requiring tight tolerances, thin walls, and deep cavities. Furthermore, because CNC machines have cylindrical tools, it can be difficult to design and cut 90-degree angles.
However, its high density, low friction coefficient, and resilient surface make it a common alternative to parts originally machined using metal. These properties contribute to Delrin’s outstanding wear resistance and ability to ensure substantial load without deforming. Moreover, Delrin has a low moisture absorption rate and high dimension retention ability, helping it maintain its shape and size when exposed to humid environments.
Delrin Applications
High Load Applications
- Gears
- Bushings
- Conveyor Belts
High Moisture Environments
- Pumps and Valves
- Piping Fittings
- Fuel System Parts
Electrical Components
- Switches
- Appliance Housing
- Coil Holders
- Electrical Insulator Parts
Delrin Properties
Property | Value |
---|---|
Density | .0513 lbs/in³ |
Tensile Strength | 75 MPa |
Flexural Strength | 80 MPa |
Elongation at Break | 25% |
Heat Deflection | 250-330 °F |
Water Absorption | .25% |
Nylon PA 12: A Brief Overview
The history of Nylon PA 12 dates to the mid-20th century when it was initially developed for traditional manufacturing processes like injection molding. Its synthesis involves the polymerization of laurolactam, resulting in a polyamide with a twelve-carbon atom backbone that contributes to its advantageous properties. According to EuroPlas, the material’s “long chains of carbon atoms provide flexibility and toughness, enabling it to withstand impact and deformation. Additionally, the repeating units of amide groups connecting to the carbon atom offer strong intermolecular interactions, resulting in high tensile strength, chemical resistance, and excellent thermal stability.”
Along with the material’s unique composition, the compatibility of Nylon PA 12 became evident with evolving 3D printing technologies including Multi Jet Fusion (MJF) and Selective Laser Sintering (SLS). Fast forward to today’s 3D printing market and it is one of the most widely used materials in the world. One reason for this is the processing capabilities of Nylon PA 12. Additive manufacturing allows engineers to design and produce complex geometries that would be difficult or even impossible to achieve with traditional machining methods.”
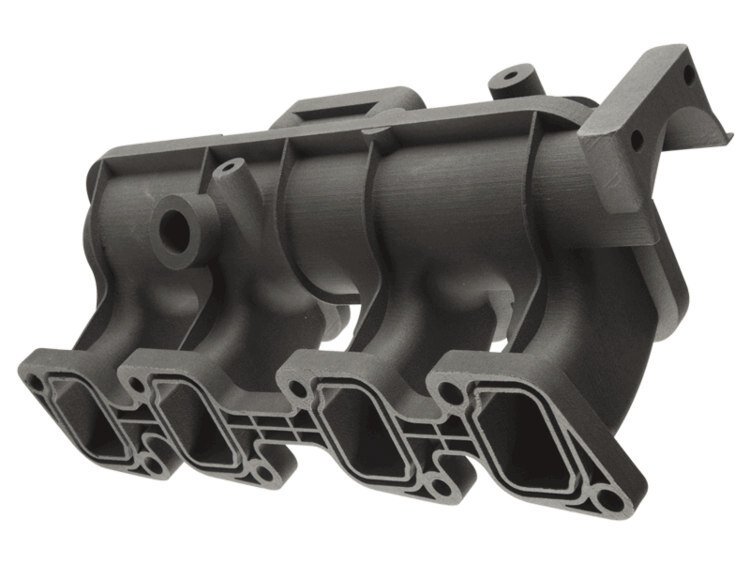
Nylon PA 12 Applications
- Under-the-hood parts
- Clips, brackets, housing, gears, and bearings
- Jigs, Fixtures, and tooling
- Manifolds
- Medical devices
- Orthotics
- Prosthetics
- Protective gear and equipment
- Thin-walled features
- Wearable devices
- Electronic casing and housing
- Drone parts
Nylon PA 12 Properties
Property | Value |
---|---|
Density | 1.01 g/cm3 |
Tensile Strength | 48 MPa |
Flexural Strength | 70 MPa |
Elongation at Break | 15-20% |
Heat Deflection | 223-347 °F |
Melting Point | 369 °F |
Nylon vs. Delrin: Conclusion
Abrasion Resistance | Moisture Resistance | High Temperature Tolerance | Complex Geometries | Low Friction | 3D Printing | Machinability | Wear Resistance | |
---|---|---|---|---|---|---|---|---|
Nylon | ✔ | ✔ | ✔ | ✔ | ✔ | |||
Delrin | ✔ | ✔ | ✔ | ✔ |