Multi Jet Fusion (MJF 3D Printing)
High-performance nylon prototype and production parts with MJF 3D printing.
Certifications:
ISO 9001: 2015
|
Get A Free Quote arrow_forwardITAR Registered
Call Us arrow_forwardWhat is Multi Jet Fusion?
The MJF 3D printing process begins with a layer of fine powder spread across the build platform, onto which a fusing agent is selectively deposited by an inkjet printhead to define the part’s geometry. A detailing agent is then applied to enhance precision, followed by the application of heat to fuse the powder, resulting in highly detailed parts with smooth surface finishes. MJF 3D printing is ideal for small to medium production runs because of its rapid build speed and high repeatability.
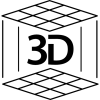
HP Multi Jet Fusion Handbook
Collaborating with Industry Leaders
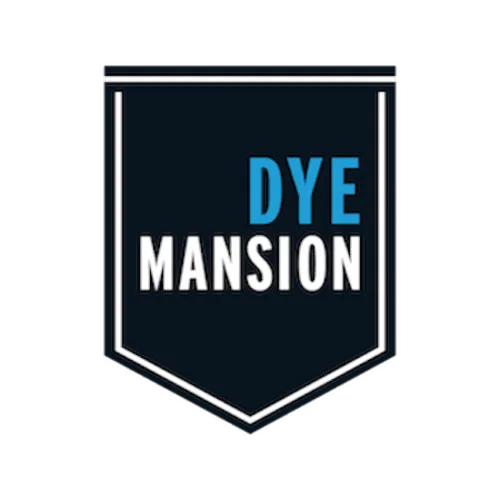
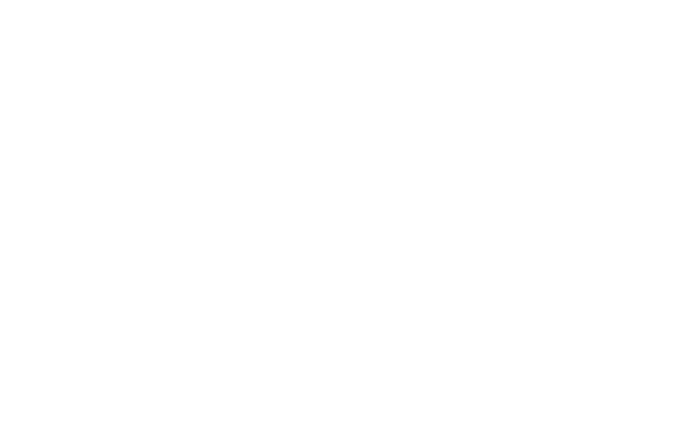
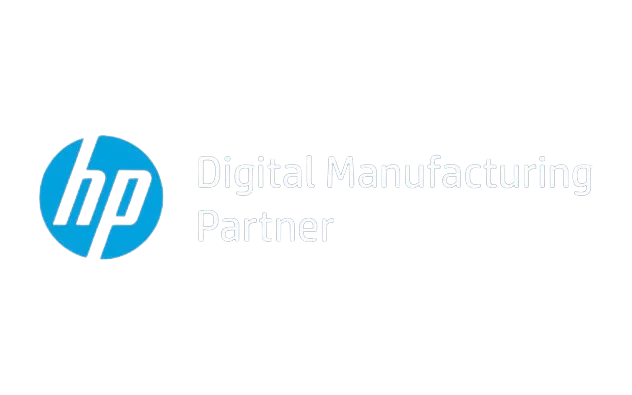

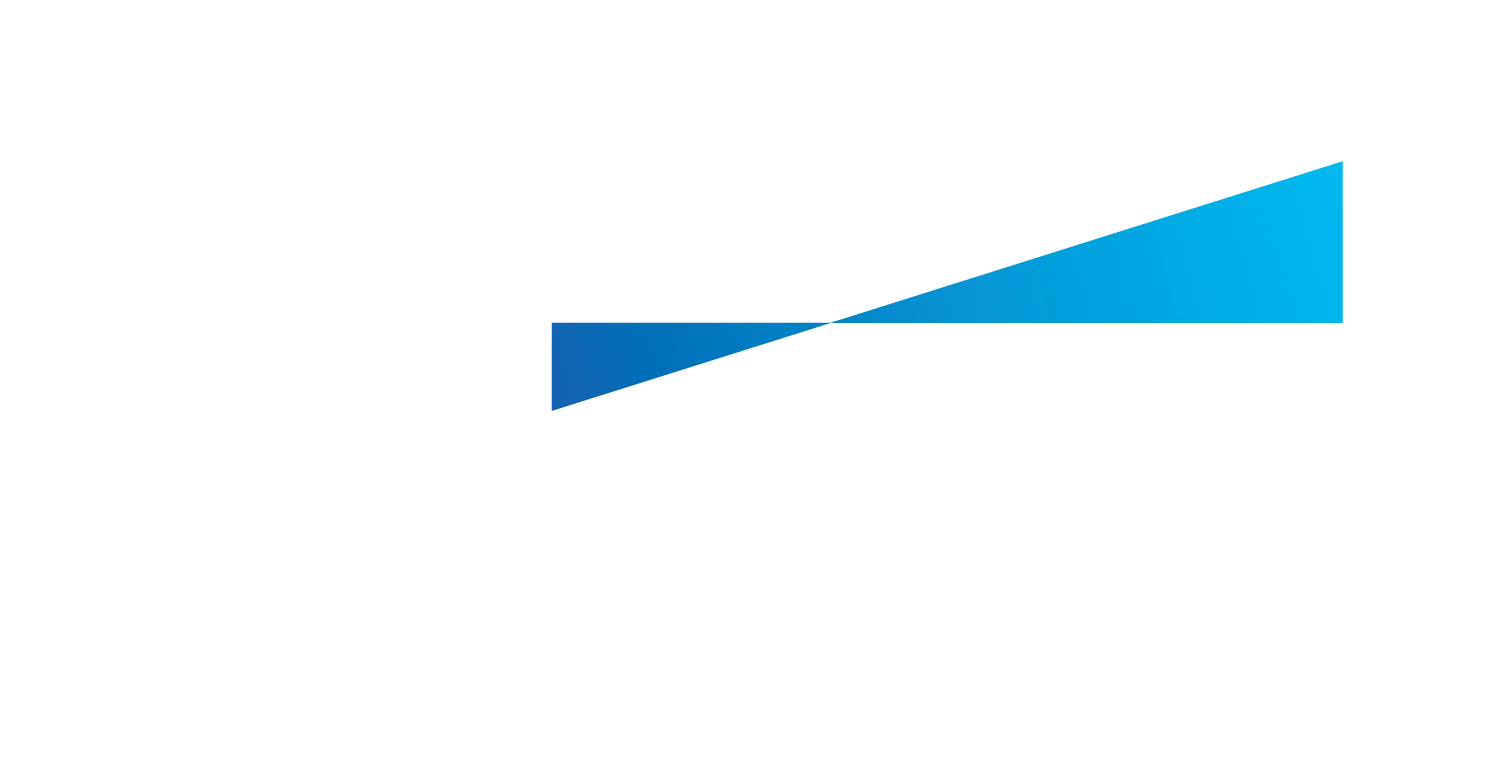
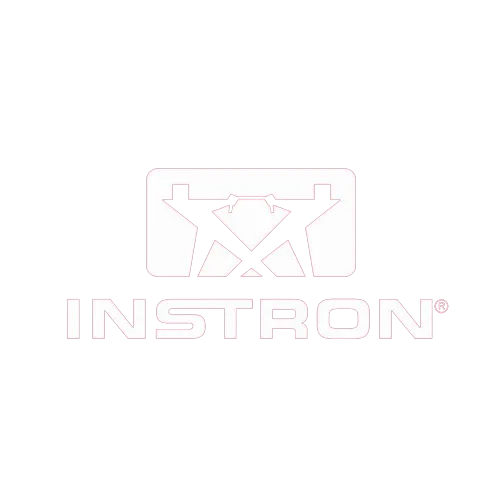
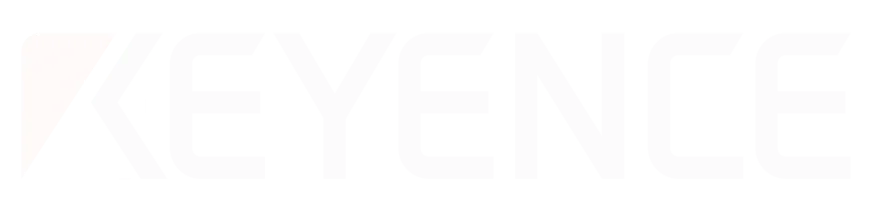
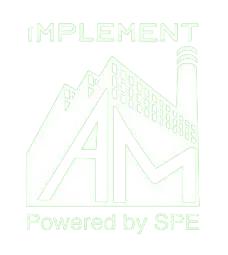
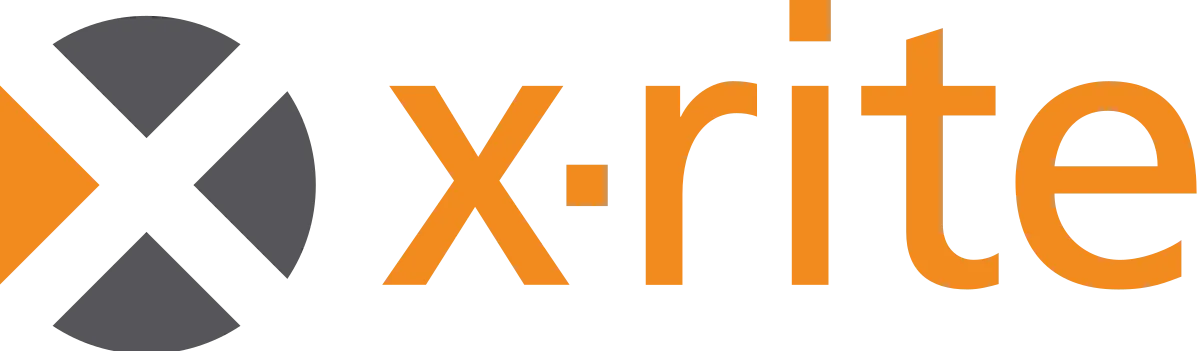

A Blend of Quality and Precision
High Precision and Detail: MJF ensures excellent surface quality and intricate detailing, achieving layer thicknesses as fine as 80 microns and dimensional tolerances of ± 0.012 in, ensuring high accuracy.
Fast Production Speed: With a high throughput, MJF 3D printing can produce parts up to 10 x faster than SLS 3D printing, making it ideal for rapid manufacturing and serial production.
Consistent Quality: MJF provides consistent mechanical properties across builds with a repeatability of ±0.3%, ensuring reliable and repeatable results.
Efficient Material Usage: MJF 3D printing with TPU material utilizes up to 80% of the material, significantly reducing waste and making it a cost-effective solution.
Less Shrinkage and Warpage: MJF utilizes a standalone cooling process, reducing the temperature gradients that cause internal stresses relating to shrinkage and warpage.
No Supports Needed: MJF eliminates the need for supports during the printing process, giving designers greater flexibility to create complex geometries and streamlining the post-processing phase.
MJF 3D Printing Design Guidelines
Warpage: Larger part sizes (>7 in.) and parts with thin features are the most susceptible to warp. We recommend maintaining a uniform thickness of 0.125 in. (3.175mm) to ensure stability.
MJF 3D printing technology can help simplify complex assemblies, overcome design constraints, and consolidate parts!
Multi Jet Fusion Material Selection
Nylon PA 12
An engineering grade thermoplastic for high-density parts with extreme dimensional accuracy and fine detail for functional prototyping and final parts. Nylon PA 12 has excellent chemical resistance to oils, greases, aliphatic hydrocarbons and alkalis.
Common Applications:
- Complex assemblies
- Lattice structures
- Housing
- Enclosures & connectors
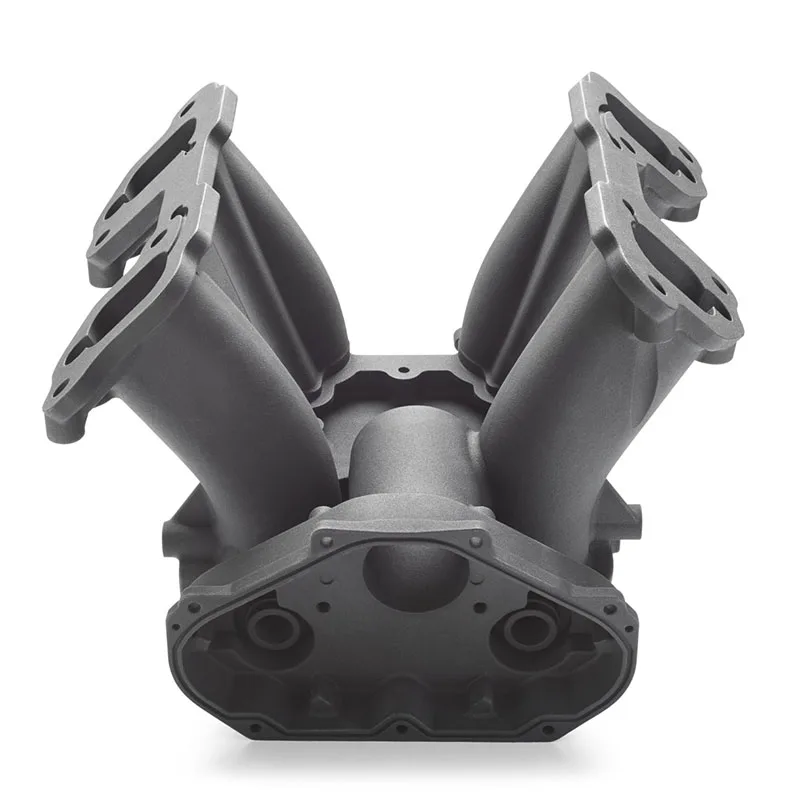
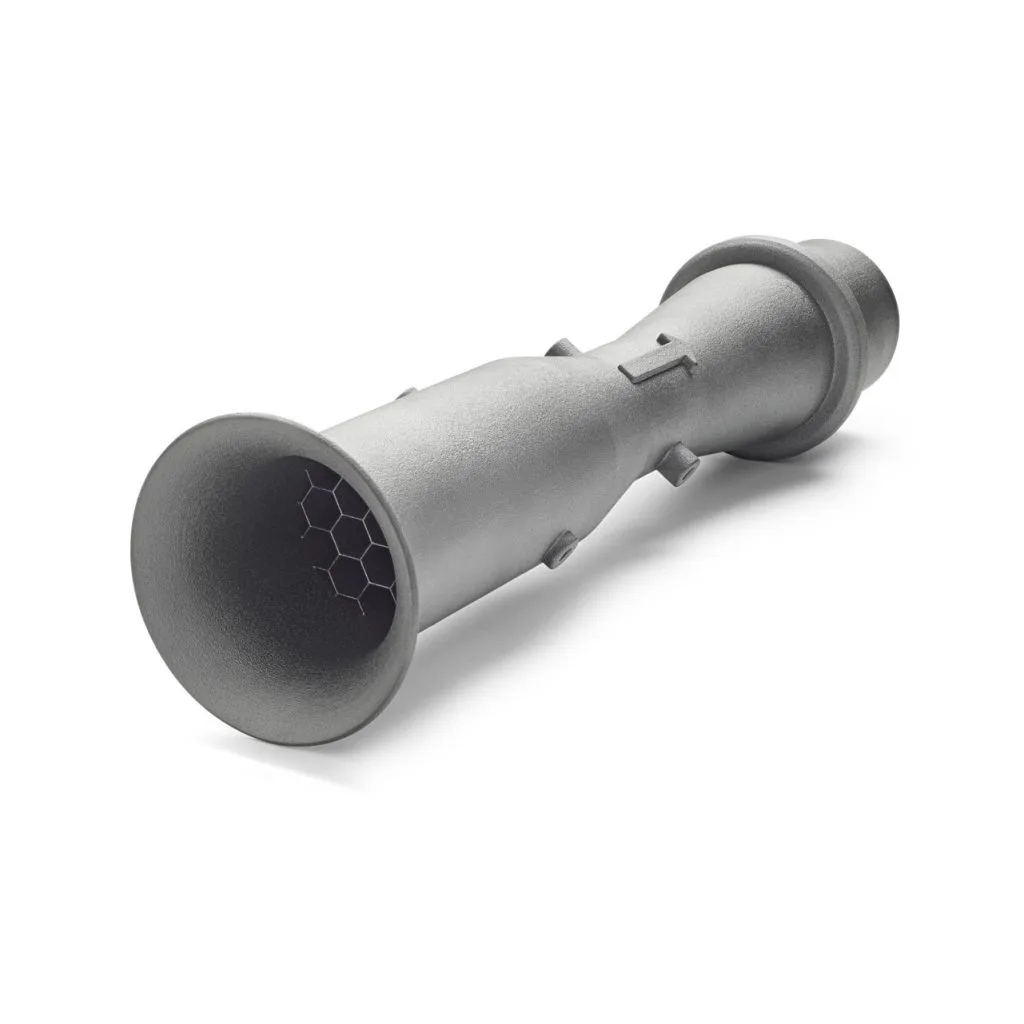
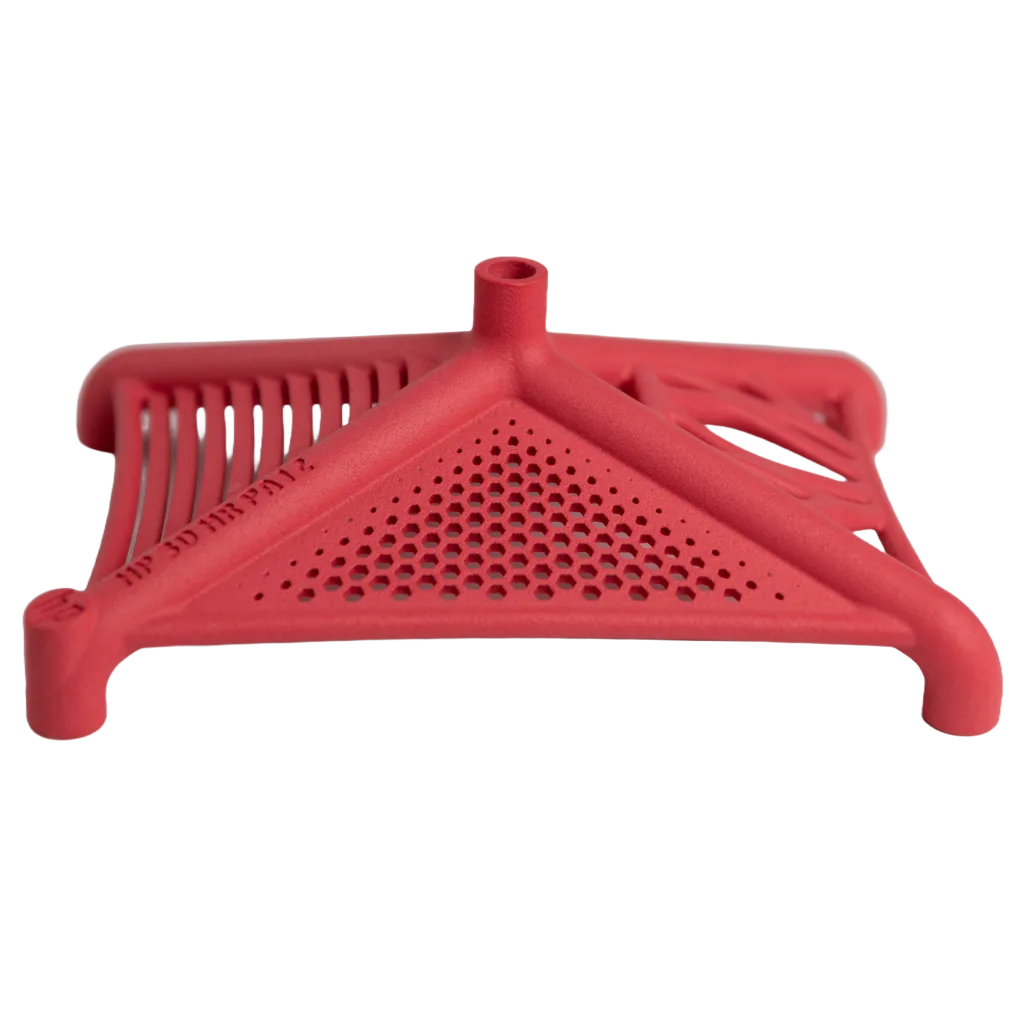
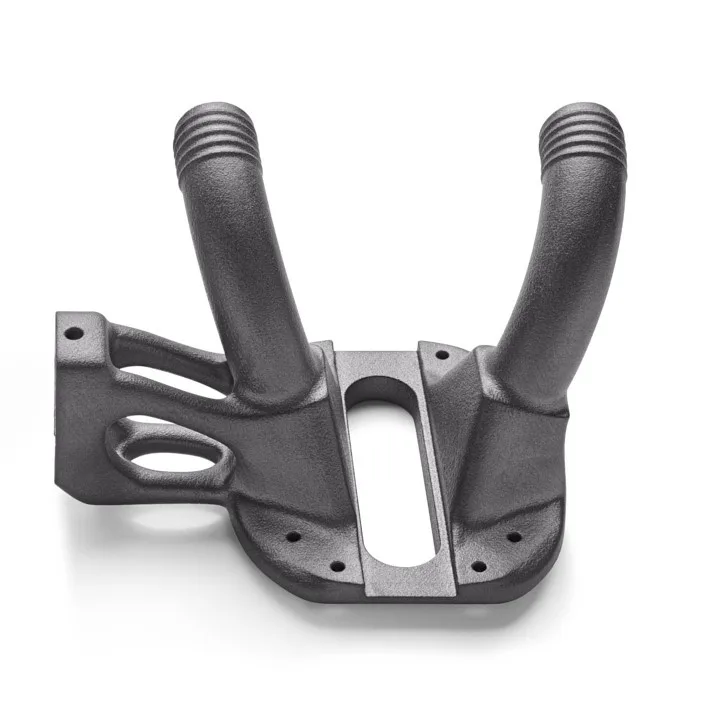
Nylon PA 12 S
Nylon PA 12 S is a thermoplastic 3D printing material engineered for multi jet fusion (MJF) technology. The material offers 70% smoother surface finish compared to PA 12 along with a reusability rate of 85%. Additionally PA 12 S reduces cost per part by up to 25%.
Common Applications:
- Dental Molds
- Consumer Goods
- Aesthetic Covers
- Volume Prototyping
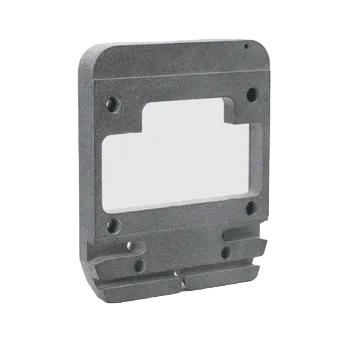
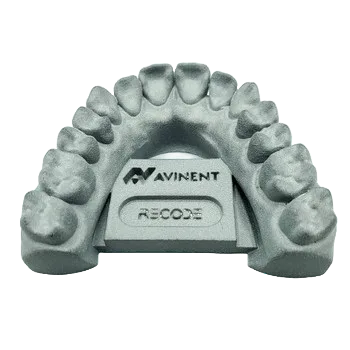
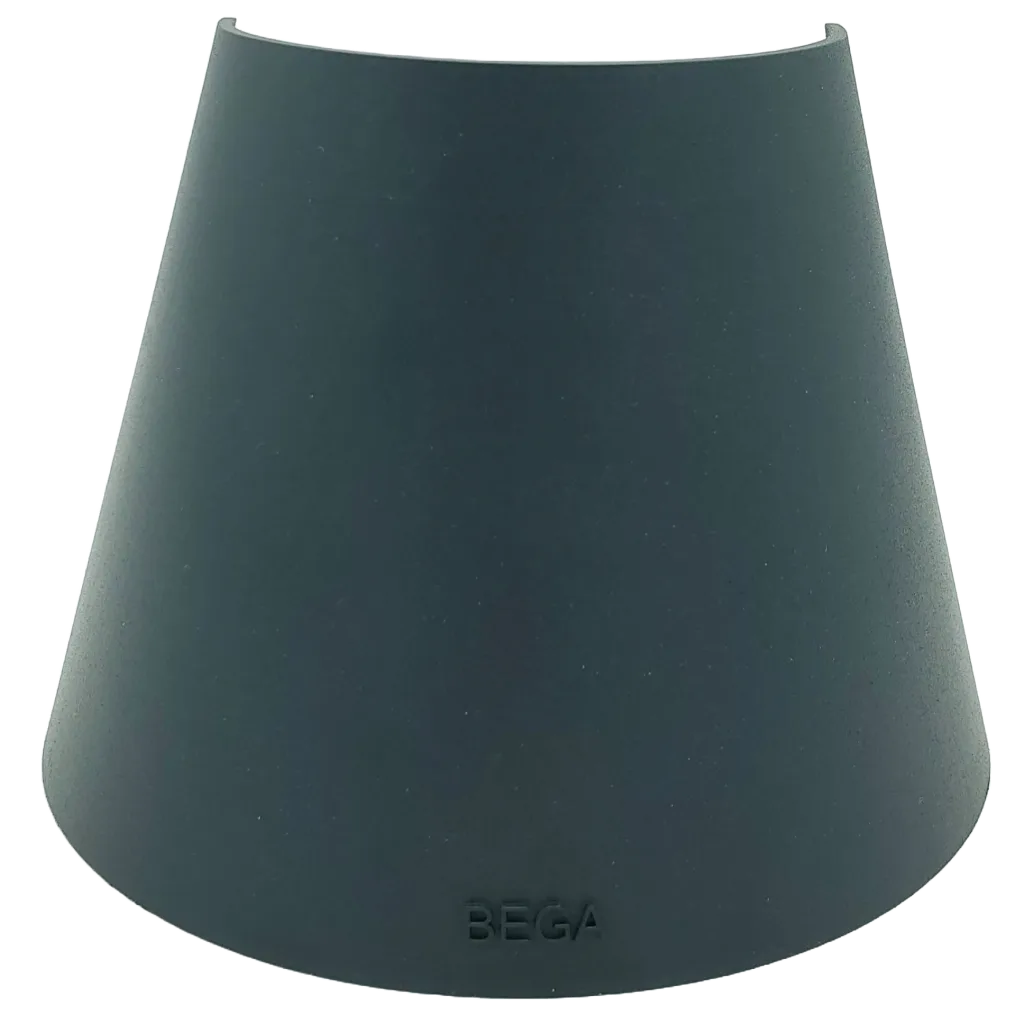
Nylon PA 12 White
This engineering-grade thermoplastic yields high-quality functional production parts in a premium white finish. PA 12 W (Pure White) is ideal for strong, complex parts with balanced property profiles and strong structures. In addition to high consistency, this robust material has high reusability.
Common Applications:
- Consumer goods
- Prosthetics & medical devices
- Fashion & wearables
- Household appliances
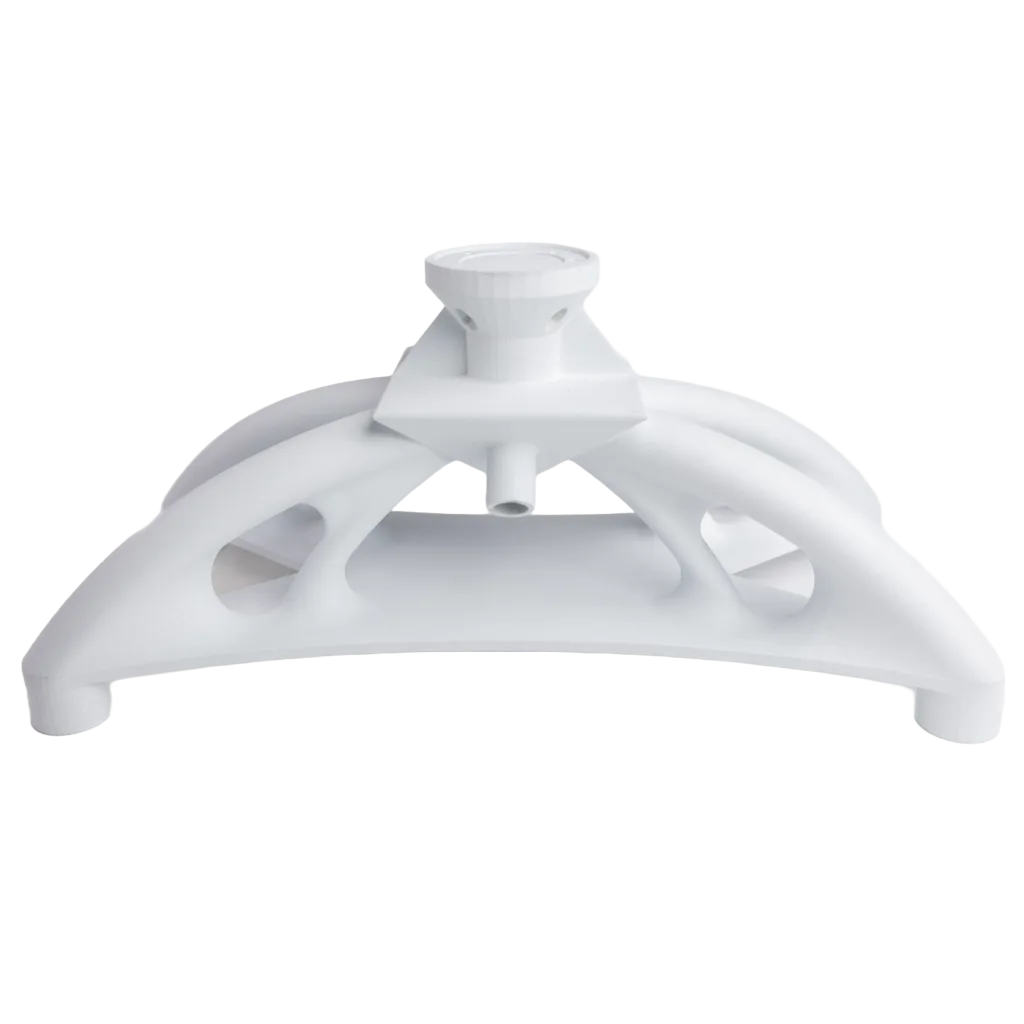
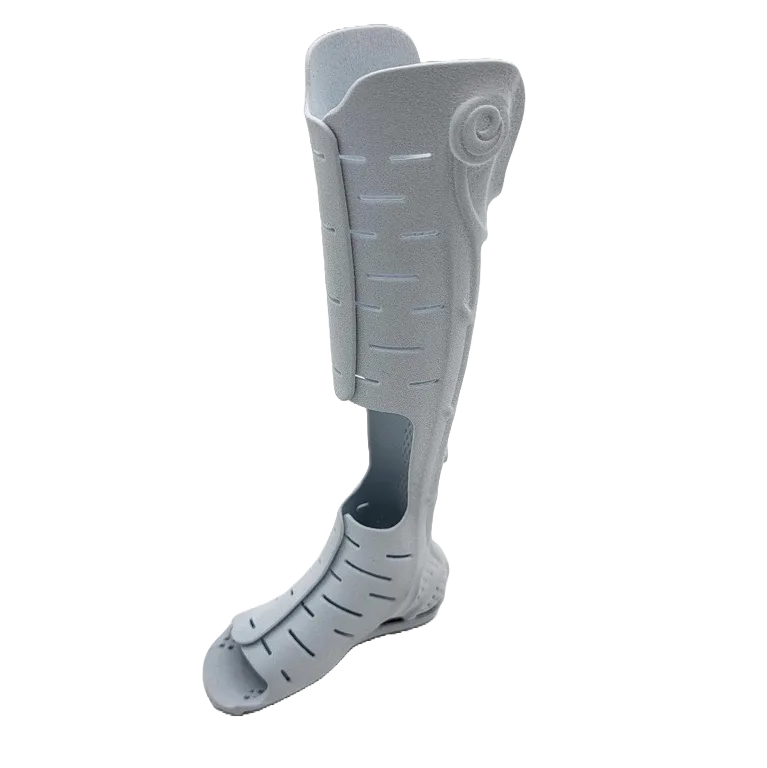
Nylon PA 12 FR
Nylon PA 12 FR is a high-performance, flame-retardant nylon material that meets UL94 V0 flammability standards at 2.5mm thickness, ensuring reliable performance in demanding environments. With a 60% powder reusability ratio, PA 12 FR minimizes waste while reducing overall production costs.
Common Applications:
- Electrical components
- Fluidic systems
- Robotics
- Machine parts
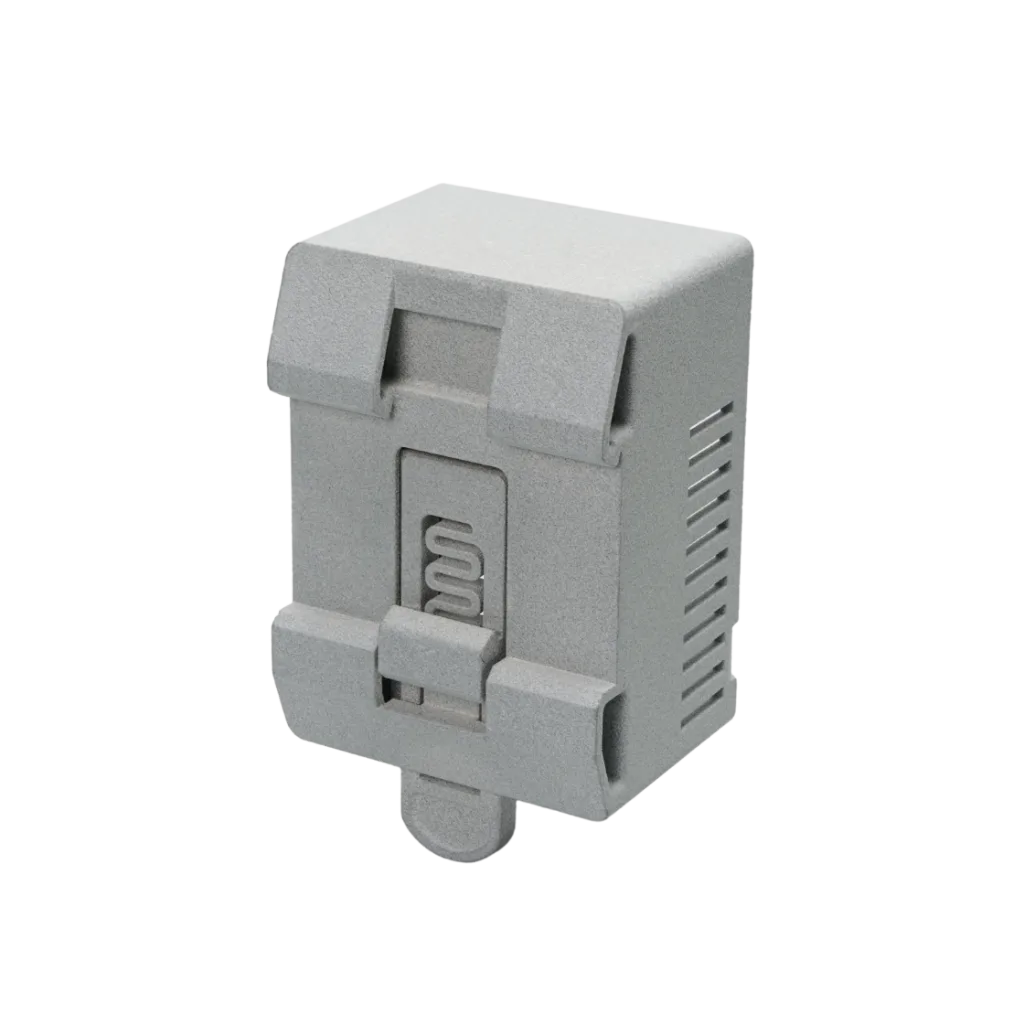
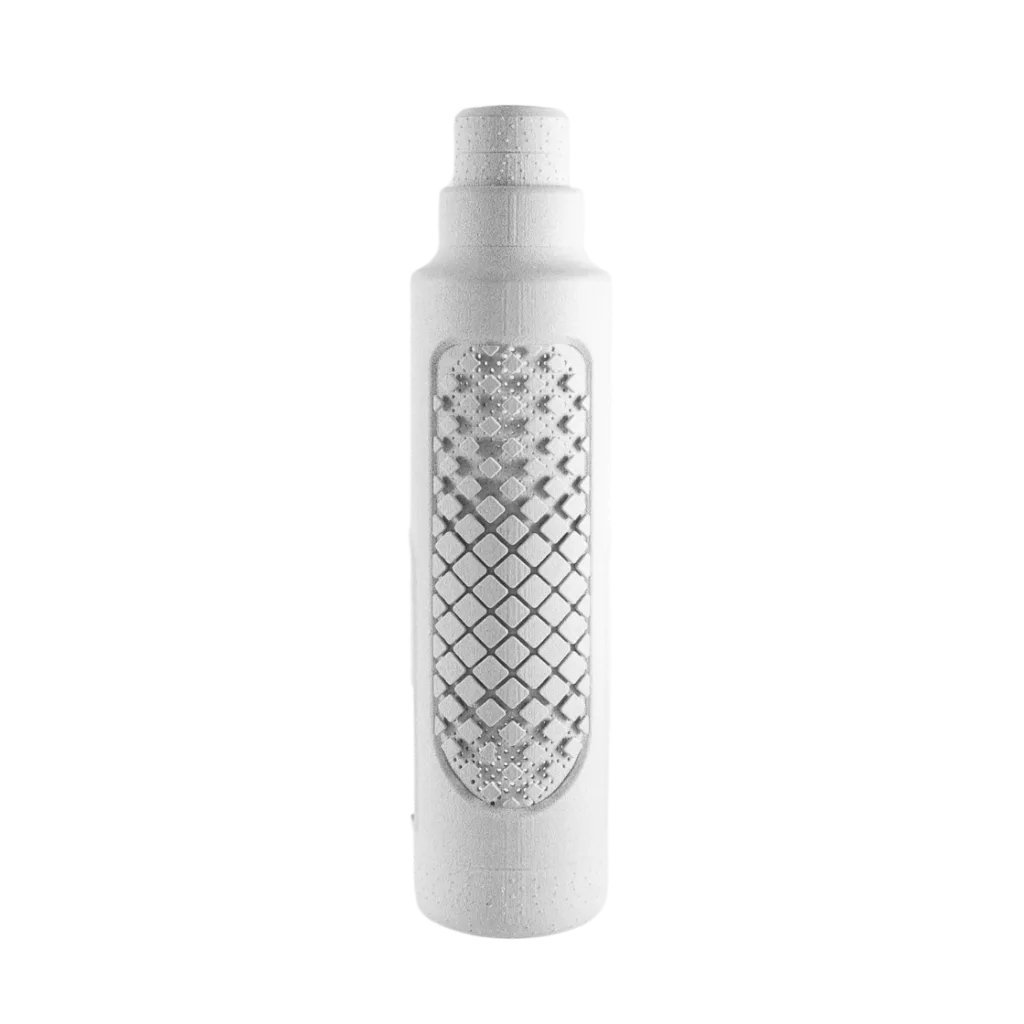
Nylon PA 11
This thermoplastic delivers optimal mechanical properties, and is known for producing strong, ductile, functional parts. PA 11 also provides excellent chemical resistance and enhanced elongation-at-break. Ideal for impact resistance and ductility.
Common Applications:
- Prosthesis
- Insoles
- Sporting goods
- Hinges
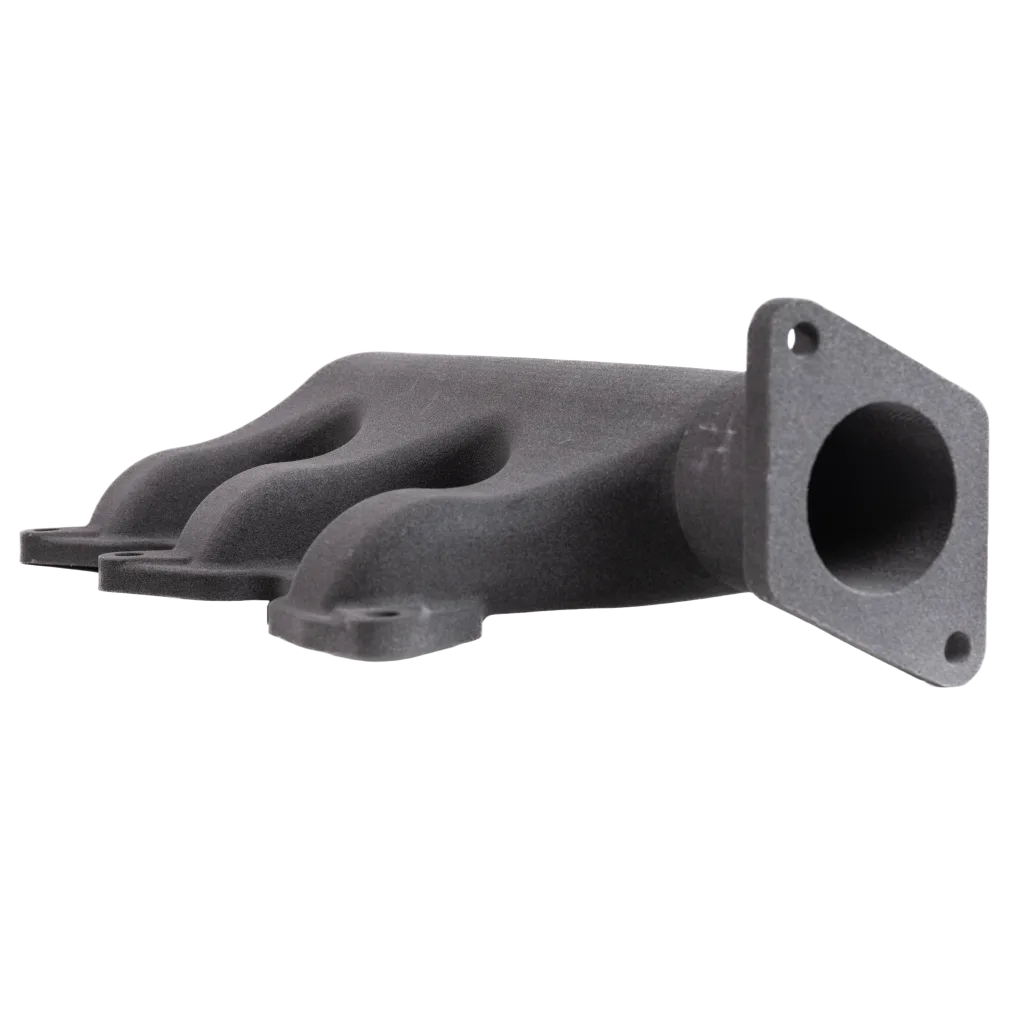
BASF ULTRASINT® TPU
This MJF specific thermoplastic from BASF offers high wear/abrasion resistance, and is ideal for applications needing rubber-like flexibility and excellent shock absorption. TPU 88A – BASF ULTASINT 3D prints with high accuracy and detail, in addition to having smooth surfaces.
Common Applications:
- Soft touch grips
- Handheld tools
- Flexible consumer goods
- Automotive hoses and wiring insulation
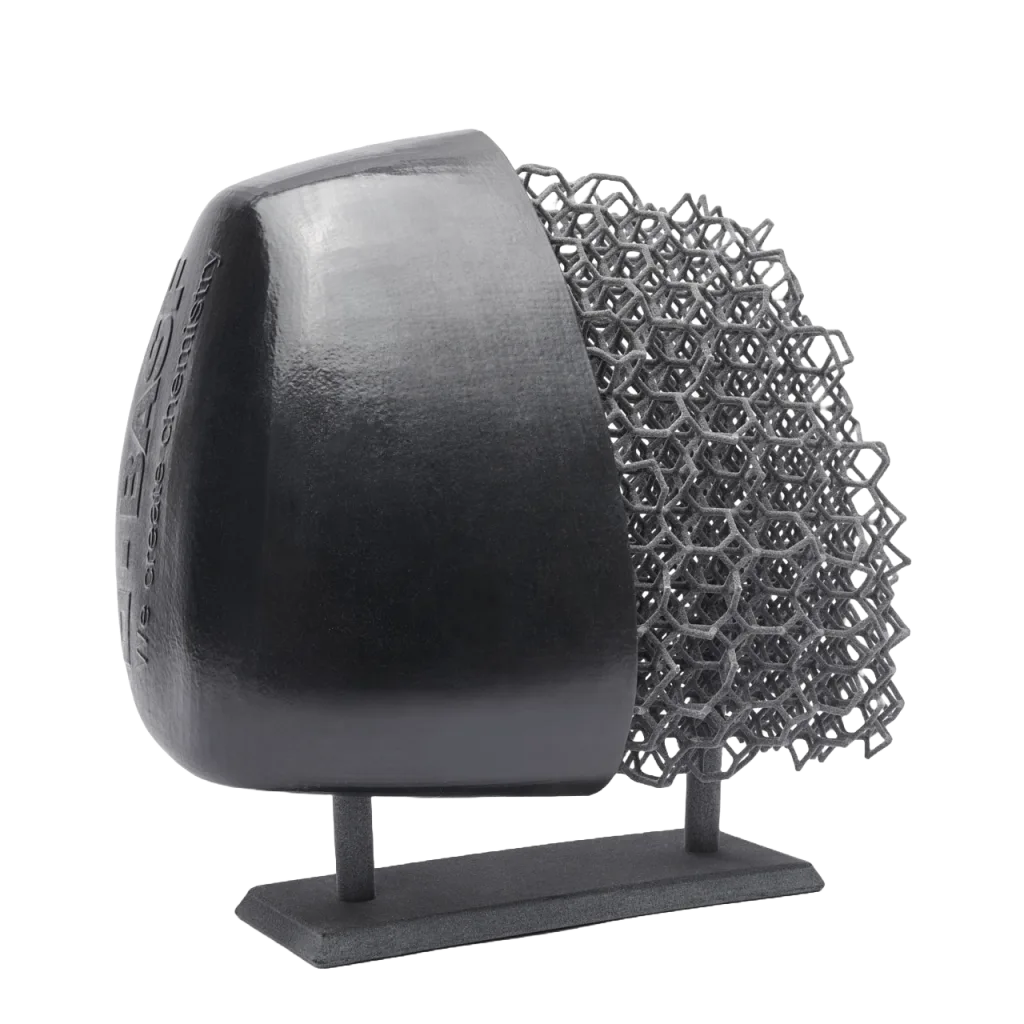
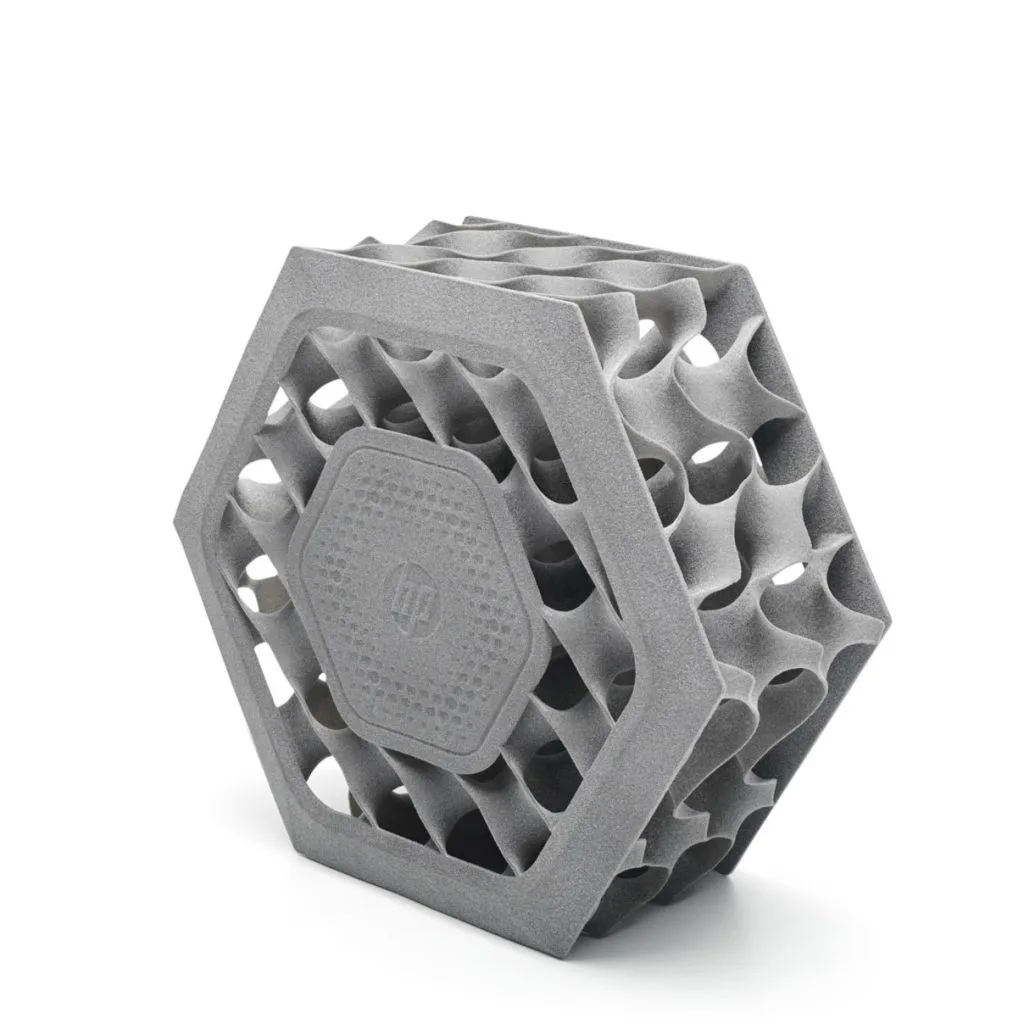
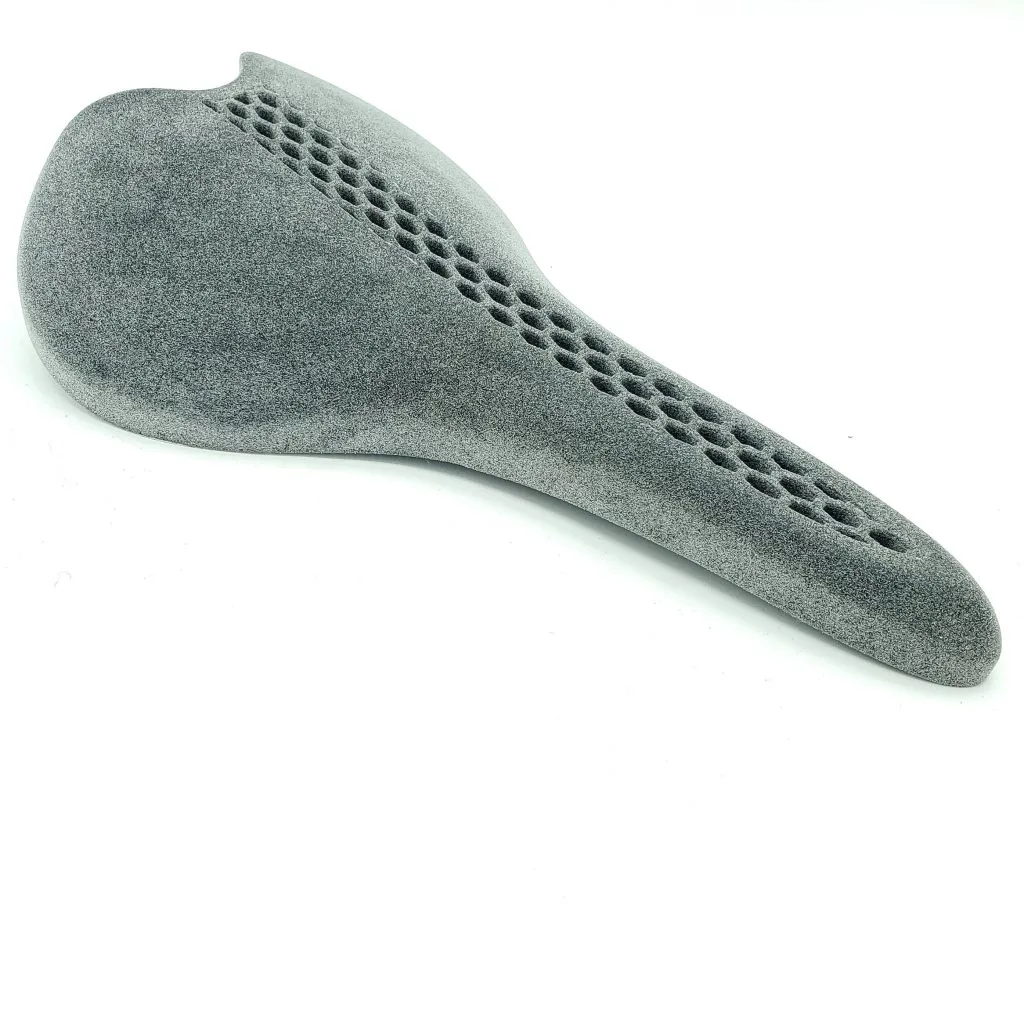
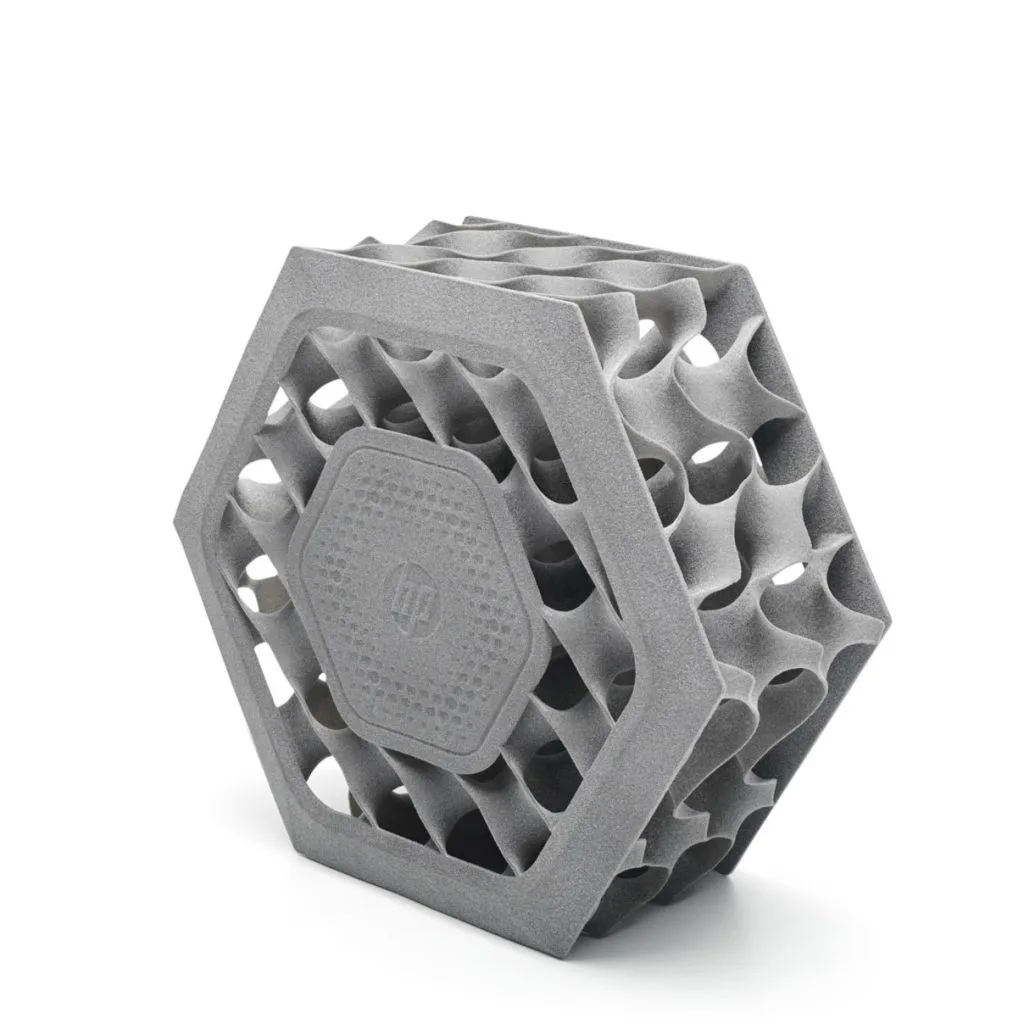
Multi Jet Fusion Surface Finish
Trusted HP DMN Partner
Endeavor 3D is proud to be a trusted HP Digital Manufacturing Network Partner and the largest contract additive manufacturer in the Southeast United States. We are recognized for our commitment to delivering high-quality 3D printing solutions using the latest HP Multi Jet Fusion (MJF) technology. This partnership reflects our dedication to meeting rigorous standards of quality, reliability, and innovation using MJF 3D printing. As an HP Digital Manufacturing Network Partner, we ensure that our customers receive parts that consistently meet their exacting requirements.
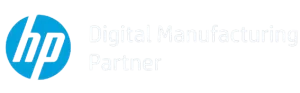
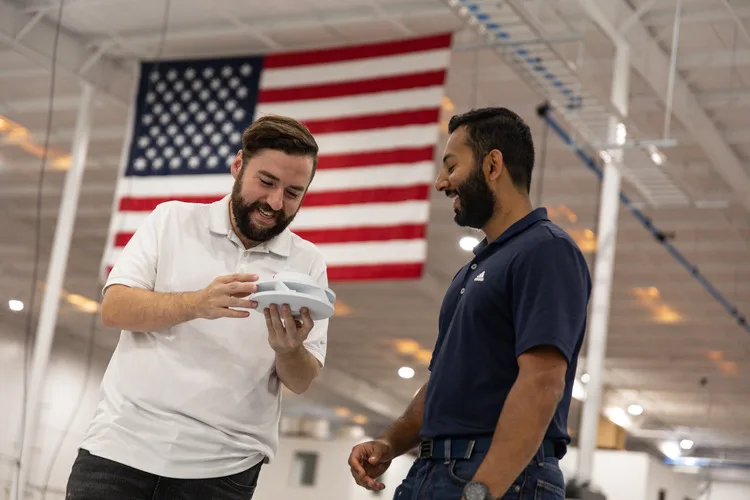