Custom Tools. Custom Wearables. Custom Colors?
3D printing is a unique tool that enables design freedom, creativity, and mass customization. By making simple adjustments in CAD and other workflow tools, designers can produce limitless custom parts that would have otherwise taken countless manual labor hours and resources (see dental 3D printing). What if we can take it one step further and bring custom colors into the mix (pun intended)?
In the following article, we will explore the value of 3D printing parts with custom colors and why we think it’s a game changer.
Understanding the Challenge
Understanding the Opportunity
Let’s dive deeper into color theory and assess how it impacts product development, provides context, adds awareness, and illicit emotions.
- Operational Communications: In any major industry, visual communication tools increase productivity and enhance safety protocols. For example, 5S, a Japanese-designed workplace organizational system, uses a five-phase system with color coding to increase productivity (sort, set-in-order, systematic cleaning (shine), standardize, and sustain). This visual system is used to improve operational efficiency and workflow. Finally, it communicates safety rules without verbal or written communication – which is highly effective for multinational assembly or production facilities.
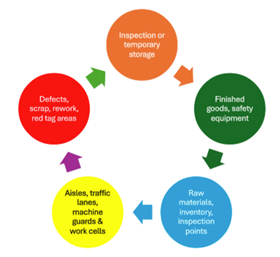
- Branding: Research has shown that a signature brand color can increase brand recognition by 80%. So, it’s no surprise that companies spend a fortune to protect their brand identity, logo, and color scheme. Mainly used to improve product appearance or aesthetic appeal, color becomes a valuable tool for designers and engineers to build products and displays that immediately catch the consumer’s eye. Remember this on your next visit to the local hardware store.
- Making a Connection: Emotions are not black and white, and neither are your products. Most product designers focus on building ergonomic, easy-to-use devices (functionality) and less time on color matching, blends, or mixtures (aesthetics). We are here to say that you can have both and can make a stronger connection with your audience. For example, many medical device products use a mixture of blue (trust), purple (ambition), and green (health) to make emotional connections with consumers. Finding the right blend could be the difference maker for your next commercial project.
Understanding the Solution
Check us out at endeavor3d.com or email us directly to start your next project – getparts@endeavor3d.com