Custom 3D Printed Drones for Last-Mile Delivery
The Basics of Last-Mile Delivery
- Optimized Cost-Efficiency: Through autonomous flight and reduced human intervention, drones offer the potential to dramatically lower the cost per parcel, estimated to be as much as 70% less than traditional delivery methods. Projections indicate a significant drop in parcel shipping costs via drone, from an estimated $60 per package in 2020 to just $4 in 2030, making them an incredibly attractive economic solution.
- Enhanced Speed and Accessibility: Drones can enhance delivery speeds and reliability, extending reach to deliver goods directly to customers’ doorsteps, often regardless of location. This capability allows organizations to reach previously inaccessible customers and ensures efficient, timely distribution across diverse geographical areas, offering comparable or even faster delivery times.
- Environmental Sustainability: Drones consume substantially less energy than conventional delivery vehicles, with estimates projecting a remarkable 94% less energy per parcel. This significant reduction in energy consumption makes drone delivery a far more sustainable option, actively contributing to a lower carbon footprint for companies utilizing this technology.
Types of Last-Mile Delivery Drones
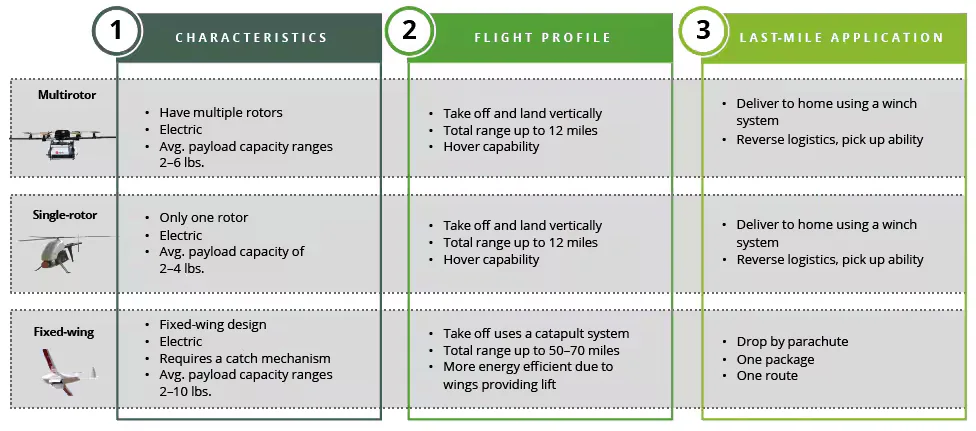
Credit: Deloitte
Challenges Facing Last-Mile Delivery Drones
- Regulatory Hurdles: One of the most significant barriers to widespread drone deployment is navigating complex and evolving aviation regulations. The Federal Aviation Administration (FAA) has established a framework of regulations and requirements to operate commercial drones for delivery purposes. One of the most known restrictions is for drones that operate beyond visual line of sight (BVLOS)—a critical capability for scalable last-mile delivery. However, countries vary widely in their drone policies.
- Limited Payload and Range: While drones excel at fast, lightweight deliveries, current battery technology restricts their operational range and payload capacity. Most commercial delivery drones are only capable of carrying 2–5 kg over short distances.
- Infrastructure and Fleet Management: A seamless drone delivery ecosystem requires more than just drones. It demands investment in launch and landing infrastructure, maintenance facilities, charging stations, and sophisticated fleet management software systems. Urban and rural geographies each pose unique infrastructure challenges, including navigating skyscrapers, tree cover, or power lines. This complicates drone routing and delivery accuracy.
How 3D Printing Supports Last-Mile Delivery Drones
1. On-Demand Spares and Repairs
Additive manufacturing can help alleviate delays in drone spares and repairs. Unlike subtractive manufacturing, Multi Jet Fusion (MJF) 3D printing builds parts layer by layer from a powder bed, using a detailing agent and fusing agent combined with thermal energy. This process provides two primary benefits that make it ideal for on-demand production:
- No Tooling Required: Because Multi Jet Fusion builds parts directly from a digital file, there’s no need for molds, dies, or machining setup. This eliminates tooling costs and dramatically reduces the time from concept to physical part.
- Digital Driven Production: Additive manufacturing allows drone OEMs and operators to store entire inventories of drone parts as 3D files rather than physical parts. The biggest benefit of this is eliminating the risk of part obsolescence. When a replacement is needed, the file is simply retrieved, printed, and shipped.
2. Digital Agility
When a design change is needed to a drone part, the CAD file can be updated and sent straight to the printer. The turnaround time between iterations is measured in days, not weeks, enabling more design loops in less time. This tight feedback loop accelerates R&D and de-risks innovation by allowing for real-world testing of design concepts early in the development process.

Collectively, the capabilities of rapid design agility, seamless file updates, and reverse engineering enable a smooth transition from prototyping to production. Since the same material and process can be used throughout the development cycle, there’s no need to requalify parts when moving from test articles to low or mid-volume production. Engineers can validate a component’s performance during prototyping and confidently scale the same geometry into production, eliminating the disconnect between the prototype and end-use part.
3. Weight Reduction Through Part Consolidation and Optimization
Unlike injection molding and CNC machining, MJF allows for the creation of geometrically complex components. Engineers can apply topology optimization, lattice structures, and part consolidation to reduce mass without compromising mechanical performance.
A prime example of this application is seen in Blueflite, a company developing advanced drone platforms specifically for logistics and emergency response. Blueflite leveraged HP Multi Jet Fusion to redesign key structural and mechanical components of its airframe. The result: a 25% overall weight reduction across their drone architecture—an outcome that directly contributes to increased payload capacity and extended flight range. In total, the drone includes 48 3D printed parts, many of which have been structurally optimized for additive production.
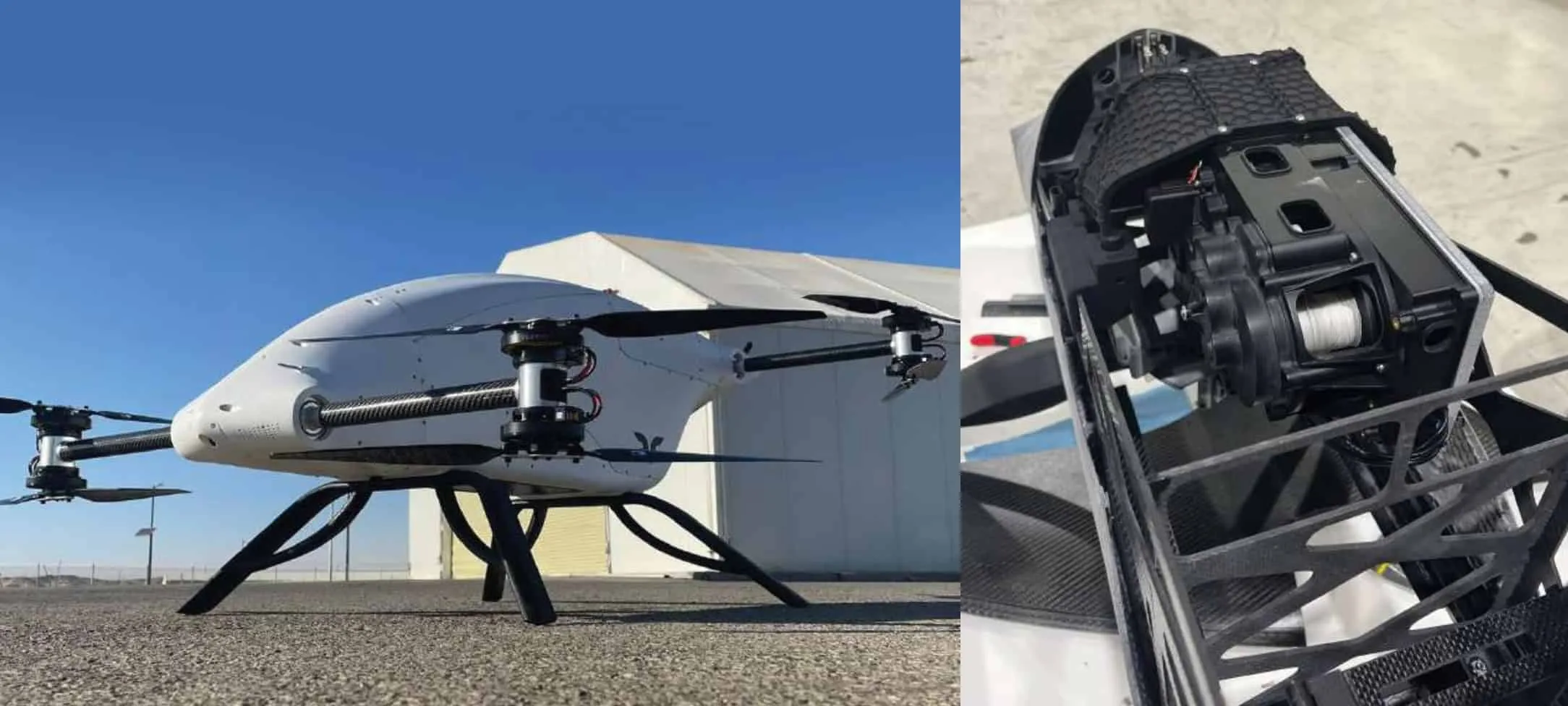
Credit: Blueflite
Conclusion
Additive manufacturing offers an opportunity to produce drone parts that are optimized for weight using specialized 3D printing materials, built without tooling, and ready for rapid iteration and deployment. With technologies like Multi Jet Fusion, manufacturers can move seamlessly from concept to production.
Submit your CAD file and get a free design review for your drone project.